
Fashion Production Process: How Clothes Get Made
Published: 4/30/2025
Fashion Production Process: How Clothes Get Made
Fashion production is a complex yet fascinating journey that turns creative ideas into garments that millions worldwide wear. Each step demands precision, collaboration, and innovative thinking—from the initial concept to the final distribution. This guide explores every stage of fashion production, outlining best practices, challenges, and essential tips.
AI Techpacks helps you generate complete techpacks using just a reference image. Streamline your tech pack creation and communicate more effectively with manufacturers. Get your first Techpack for free!
Let’s dive in.
1. Concept and Design Development
The fashion production process starts with conceptualization and design development. It is important to have strong project management for your clothing line. This stage is about transforming creative visions into viable designs that align with market trends and consumer expectations.
Inspiration and Trend Research
You can find inspiration in everything from historical fashion and art to nature and cultural events. Trend forecasting is also crucial for staying relevant. Platforms like WGSN and Fashion Snoops help brands predict upcoming styles, colors, and fabric choices to stay ahead of consumer demand.
Sketching and Digital Design
While many designers still begin with traditional sketches, computer design tools like Clo3D have become invaluable. They make it easy to create precise illustrations, experiment with color schemes, and even visualize garments in 3D. These digital solutions accelerate the design process and simplify revisions before production begins.
Technical Drawings and AI-Assisted Tech Packs
After finalizing a design, tech packs for clothing are made for manufacturers to capture essential details—like measurements, stitching specifications, and fabric requirements. AI Techpacks automates the creation of these detailed tech packs. It significantly reduces manual input, helps you reduce errors, ensures clear communication with factories, and speeds up production timelines. Get your first tech pack for free.
2. Pattern Making and Prototyping
Once a design is set, the next step is pattern making and prototyping. This is where designers confirm that the garment fits correctly and reflects their vision. Patterns determine each piece of fabric’s shape and dimensions.
A well-crafted pattern can make the difference between a smooth production run and costly manufacturing mistakes.
Pattern Creation
While traditional pattern makers use paper templates, many brands now prefer digital software like Gerber AccuMark or CLO 3D to produce and grade patterns more accurately. These modern solutions also factor in fabric behavior, such as stretch, drape, and shrinkage, along with seam allowances and stitch details.
Digital vs. Manual Pattern Making
Manual pattern making remains popular in couture and luxury fashion, where customization is vital. However, digital methods offer several advantages.
- Faster Development: Quick changes and adjustments.
- Less Waste: Virtual testing reduces fabric use.
- Simple Grading: Easy to scale patterns to multiple sizes.
Sampling and Fittings
Before full-scale production, designers create a sample (often called a toile or muslin) to test the garment’s structure and fit. The process usually follows these steps.
- First Sample: Evaluated for overall construction.
- Fit Tests: These are conducted on mannequins or live models to check proportions and comfort.
- Revisions: Additional samples may be needed until the garment meets the brand’s standards.
AI-driven tools can assist by simulating fit and identifying potential issues before a physical prototype is made, saving time and materials.
3. Sourcing Materials & Ethical Considerations
After finalizing the design and prototype, the next important step is sourcing the materials that bring your vision to life. This involves selecting fabrics, trims, and other components with an eye on quality, cost-effectiveness, and sustainability.
Choosing Fabrics and Trims
Weigh the following factors.
- Fabric Composition: Whether to use natural fibers (cotton, wool, silk) or synthetic ones (polyester, nylon, spandex).
- Texture and Weight: How the fabric drapes and fits against the body.
- Durability and Care: Some fabrics demand delicate handling, while others can withstand heavy wear and tear.
Fabric selection is one of the most critical decisions in garment production. Trims such as zippers, buttons, and other decorative elements must also be chosen thoughtfully to enhance the garment’s functionality and overall design.
Sustainable and Ethical Sourcing
Today, ethical sourcing is a major focus in fashion as environmental and social concerns gain prominence. Many brands are now doing the following.
- Using Eco-Friendly Materials: From organic cotton and recycled polyester to plant-based dyes.
- Partnering with Responsible Suppliers: Ensuring fair labor conditions and transparent supply chains.
- Minimizing Waste: Embracing zero-waste patterns or upcycled fabrics.
Some companies use blockchain tools to trace the origins of their materials, giving consumers clear visibility into where and how items are produced. Brands like Everlane and ISTO have built their reputations around transparency and responsible sourcing, underscoring the growing consumer demand for sustainable fashion.
Balancing Cost and Sustainability
While ethical materials can be pricier, technologies are rapidly driving down these costs. Brands can balance profitability with sustainability in the following ways.
- Adopt On-Demand Production: Manufacture garments only after orders are placed to avoid surplus stock.
- Explore Alternative Fabrics: Hemp, bamboo, or lab-grown options may offer eco-friendly benefits with competitive pricing.
- Build Partnerships: Many suppliers offer bulk discounts for sustainable materials, making larger orders more cost-effective.
The next stage will bring your design closer to the final product.
4. Manufacturing & Production
The garment is ready for mass production with designs approved, patterns perfected, and materials sourced. This phase is typically the most resource-intensive, relying on skilled labor, specialized machinery, and well-structured workflows to achieve consistent quality.
Cutting and Sewing
Manufacturers begin by cutting fabric according to the approved patterns. This can be done manually with precision cutters or through automated cutters for heightened accuracy. The cut pieces then move on to sewing stations, where they’re assembled into finished garments.
Sewing can involve the following.
- Manual Stitching: Common in high-end or couture fashion, requiring skilled labor for detailed work.
- Automated Assembly: Used by larger brands to increase production speed and uniformity.
Factors such as budget, production volume, and the garment’s complexity determine whether brands favor manual or automated methods.
Mass Production vs. Small-Batch Manufacturing
Brands follow different scales and methods.
- Mass Production: Fast-fashion giants like Zara and H&M rely on large factories, bulk materials, and global supply chains to produce enormous volumes quickly.
- Small-Batch Manufacturing: Preferred by independent and sustainable brands looking to reduce waste, allow for customization, and maintain tighter quality control.
- White Label Manufacturing: Common among emerging brands and entrepreneurs looking to quickly enter the market with minimal overhead. These manufacturers produce generic, unbranded products that businesses can rebrand and sell as their own. It enables speed-to-market, reduces development costs, and allows non-technical founders to launch product lines without managing production. However, customization options are limited, and product differentiation can be challenging.
Ethical and Sustainable Production Practices
With consumers demanding ethical accountability, manufacturers are gradually adopting sustainable production practices.
- Fair Labor Standards: Ensuring safe working conditions and living wages.
- Eco-Conscious Methods: Low-waste cutting, waterless dyeing, and renewable energy sources.
- On-Demand Production: Making garments only after they’re sold to cut down on overstock.
5. Quality Control & Finishing
Once the garments are assembled, they undergo quality control and finishing to ensure they meet the brand’s standards and customer expectations.
Ensuring Consistency and Durability
During quality control, garments are checked for the following.
- Stitching Integrity: Identifying loose threads, uneven seams, or fabric flaws.
- Accurate Measurements: Verifying that each piece matches the approved sample in terms of size and proportions.
- Color Consistency: Making sure dyes and prints are uniform across all items in a batch.
- Durability Testing: Confirming that zippers, buttons, and fastenings withstand normal wear and tear.
Luxury and high-end fashion brands often conduct multiple rounds of inspection to preserve their reputation for excellence.
Final Touches
After the garments pass inspection, they move to the finishing stage, where final adjustments are made.
- Pressing and Steaming: Removing wrinkles and ensuring the garment drapes correctly.
- Labels and Branding: Attaching size tags, washing instructions, and brand labels.
- Special Treatments: Applying embroidery, embellishments, or fabric distressing.
- Packaging: Folding or hanging garments and preparing them for shipment in eco-friendly packaging materials.
Many brands are choosing sustainable packaging methods—like biodegradable bags, recycled paper tags, or reusable wrapping—to reflect their commitment to reducing environmental impact.
6. Logistics & Distribution
The garments need to be efficiently stored, shipped, and delivered. This phase is crucial because it affects delivery timelines, stock availability, and overall customer satisfaction.
Inventory Management & Order Fulfillment
Effective inventory management is key to balancing supply and demand. Many brands use enterprise resource planning (ERP) systems to track stock levels, forecast sales, and coordinate warehouse operations.
Once packaged, products can move through various distribution channels.
- Retail Distribution: Sent to brick-and-mortar stores, department shops, or specialized boutiques.
- E-commerce Fulfillment: This typically involves storing inventory in a warehouse or using third-party logistics providers (3PL) for direct-to-consumer shipping.
- Wholesale Distribution: Involves selling garments in bulk to other retailers.
Direct-to-consumer (DTC) brands place special emphasis on last-mile delivery, which is the step from the warehouse to the customer door. Technology-driven solutions like those offered by Amazon and Shopify help optimize routes, shipping costs, and speed.
Sustainable Packaging & Shipping
Like almost everything else, eco-friendly logistics are on the rise as brands seek to lower their carbon footprint. Approaches include the following.
- Biodegradable Mailers: Reducing plastic waste in shipping materials.
- Carbon-Neutral Delivery: Offsetting emissions through green initiatives.
- Local Production & Fulfillment Centers: Shortening supply chains to minimize transportation impact.
Some companies even adopt on-demand production models, such as manufacturing goods only after receiving orders, to reduce surplus inventory.
Create Your Tech Pack in No Time with AI Techpacks
The fashion production process can be intricate, but with the right tools and planning, it doesn’t have to be overwhelming. Tech pack creation remains crucial for ensuring accuracy and clear communication with manufacturers.
With AI Techpacks, you can generate precise tech packs using just a reference image. Our platform automates key details so you can bring your designs to life faster. Get your first tech pack for free.
Get in Touch
Have questions or need support? Contact us at
info@muse.place.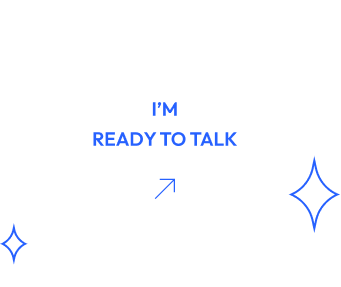
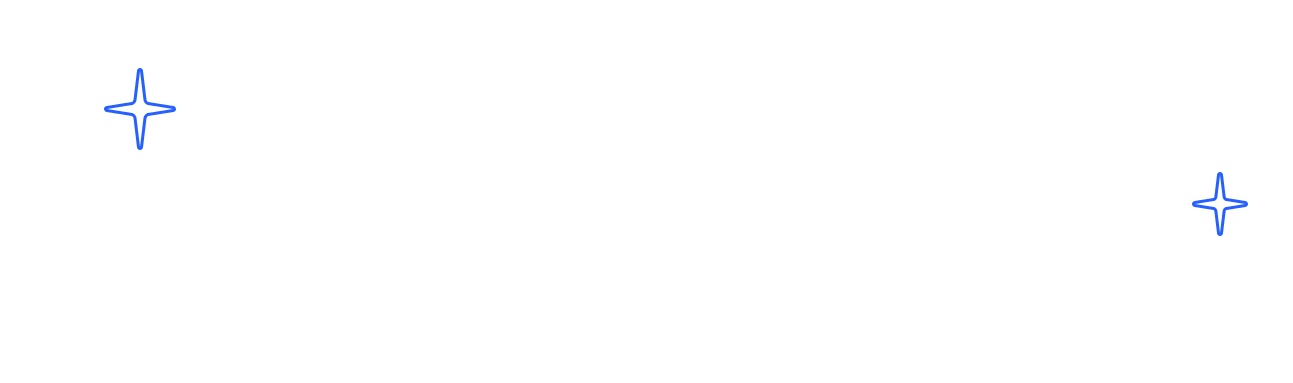
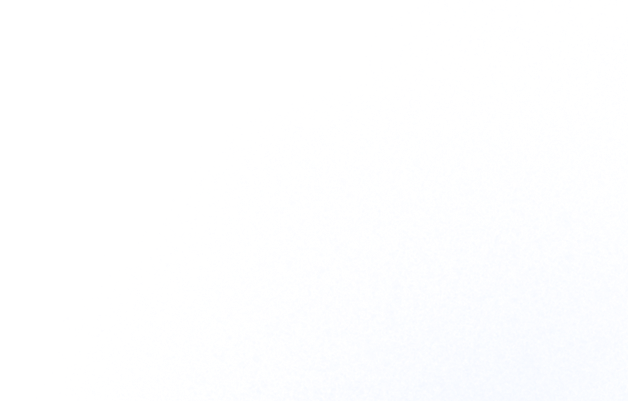
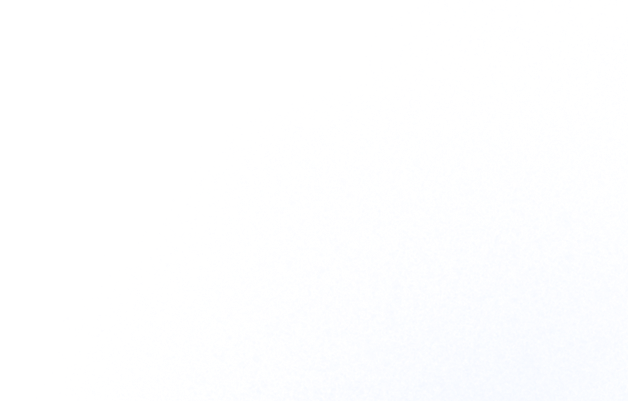